In Fine Form
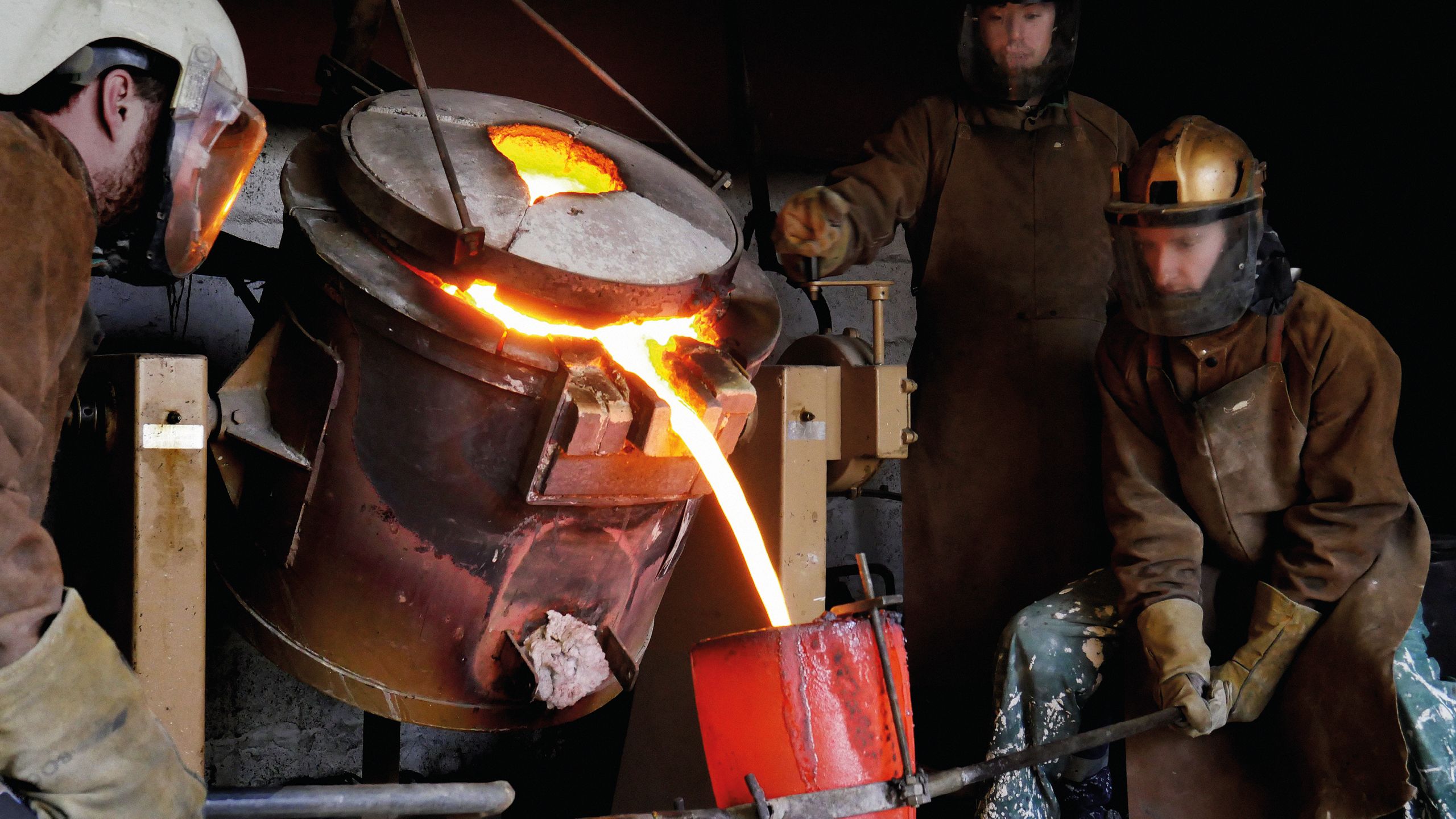
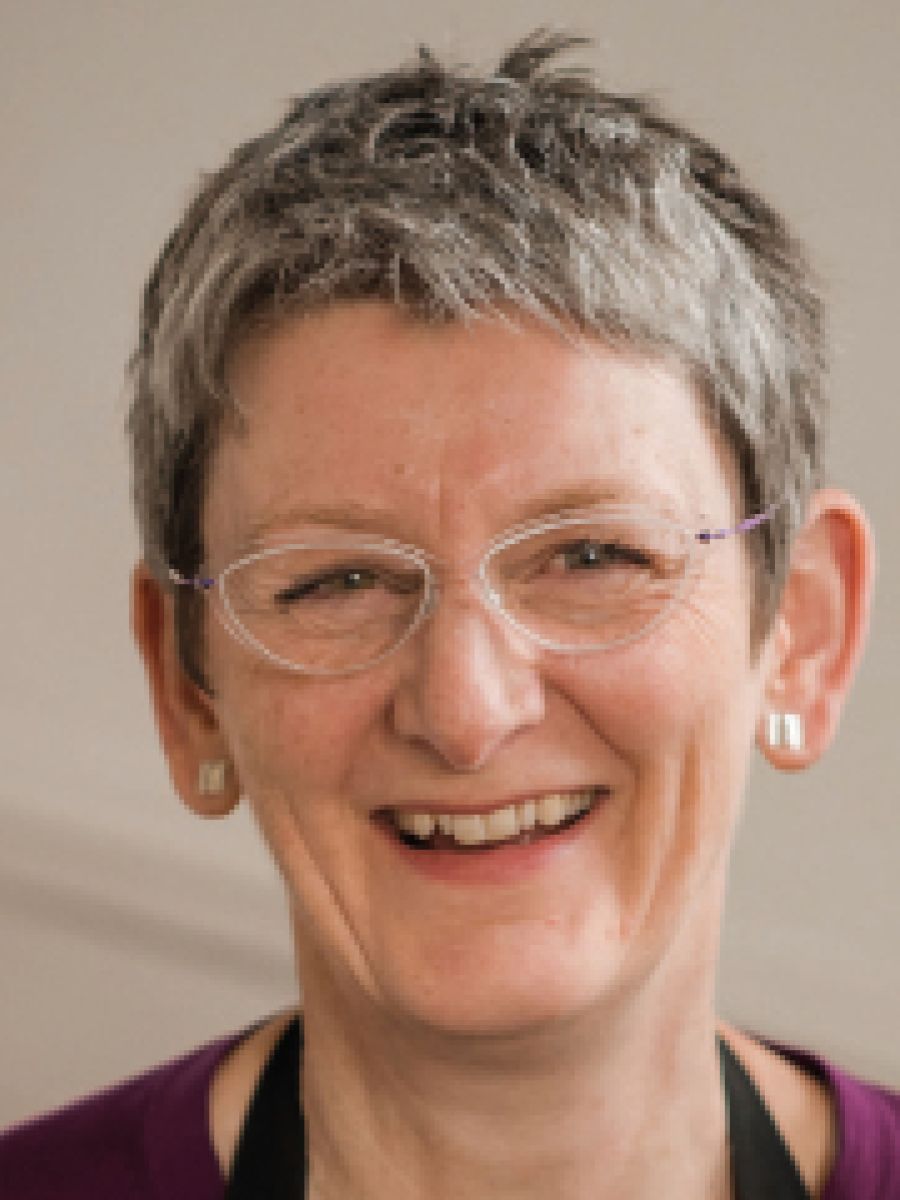
Ann Shearer: Former Vice-Dean of the Dental Faculty, now designing and making jewellery in Edinburgh
Ann Shearer: Former Vice-Dean of the Dental Faculty, now designing and making jewellery in Edinburgh
The businesses featured here are not individual artists in their studios, but instead a mill and a foundry, both of which are essential to the process of creating art and for the maintenance of key craft skills.
The Paper Foundation
The Paper Foundation was launched as a charity in 2018 by Mark Cropper when he realised that the skill of making paper by hand was a dying art. The aim of the foundation is to sustain the craft and skills of paper-making, celebrate paper arts and heritage, and protect the handmade paper product.
Cropper is Chair of James Cropper, a commercial paper company based in Burneside in the Lake District that employs 600 people and produces luxury coloured paper. On learning that the Griffen Mill in Ireland was about to close with no successors, he opened a handmade-paper mill in a converted cowshed in Burneside to house Griffen Mill’s equipment alongside other pieces he had salvaged from old mills around the country.
He also employed Tom Frith-Powell – a history graduate with no paper-making experience, but with enthusiasm and some local knowledge – to learn the craft from the Griffen makers. Frith-Powell now makes book and conservation paper, which is used for new book spines, repairing torn pages and replacing missing pages. The demand for such paper comes from museums and libraries worldwide such as the Vatican and the British Museum. Conservation paper has to be a sympathetic match to the original and Frith-Powell achieves this by knowing the history of the book, where and when it was made, adjusting the fibre type and handling as required.
"The aim of the foundation is to sustain the craft and skills of paper-making heritage"
Paper is made from any plant fibre that contains cellulose. Traditionally, clothing rags of linen, cotton or hemp are beaten to pulp with water. Frith-Powell uses a Hollander beater (named after its country of origin where it was invented in the 17th century) to macerate the fibre with water until it becomes pulp. This is then scooped into a mould, which is gently shaken to form a single sheet. The layer of pulp is then moved from the mould onto a sheet of woollen felt. This action is known as couching. The layers are stacked into a press to squeeze out excess water and after three pressings, one in felt and two as a stack of paper, the sheets are hung up to dry.
The moulds are wooden trays with open slats, historically made in South American mahogany, as it can cope with constant wetting and drying without warping. Cropper has collected more than 800 moulds from old mills, 90% of which are still usable. Many have a wire image sewn into the base to give thinner areas of paper to create a watermark. The watermarks are of company logos such as banks, and the paper would be used for share certificates.
Cropper has long-term plans to build a new handmade-paper mill in the village next to the existing modern mill. In the meantime, he has opened a paper-making archive in a former Cropper family home, which is open by appointment.
For more information or to buy sketchbooks and watercolour paper go to www.paper.foundation
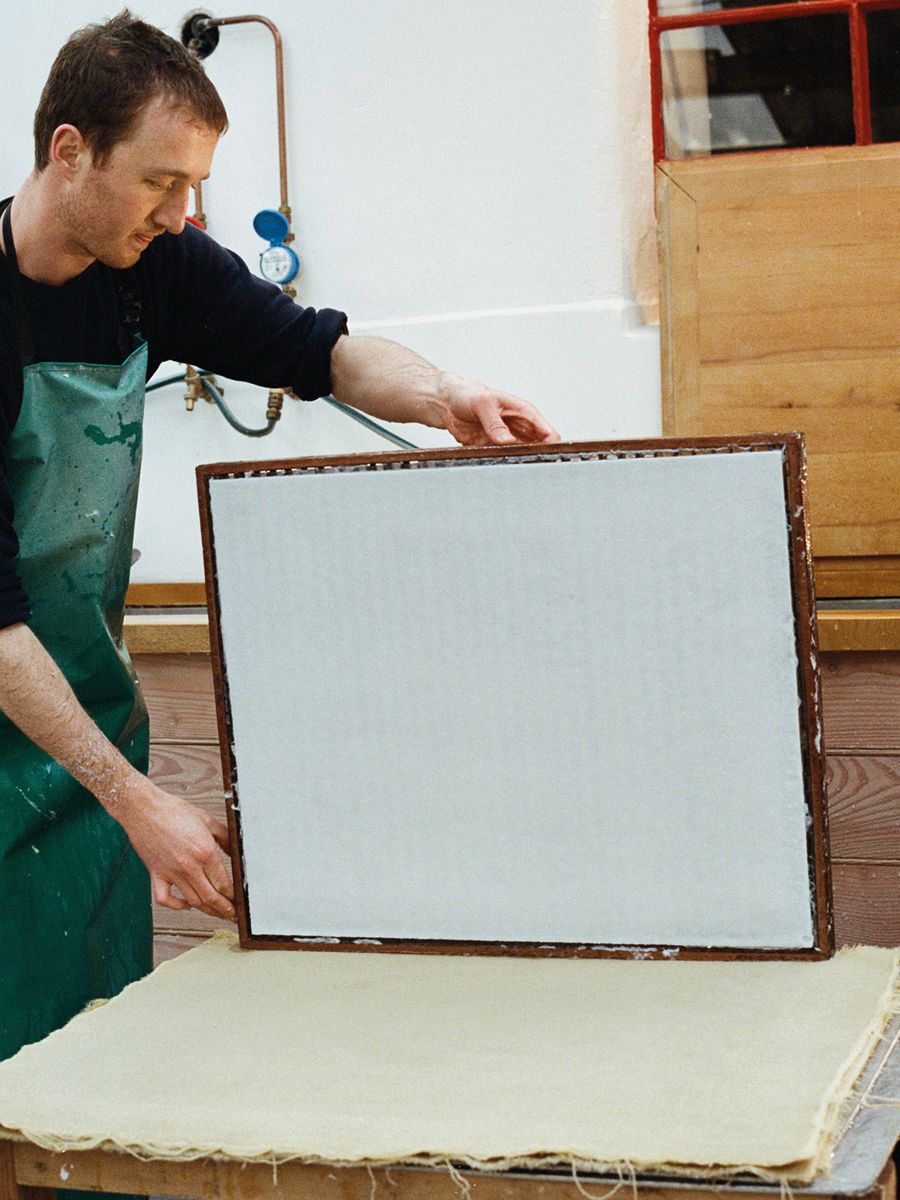
Tom Frith-Powellat work at the Paper Foundation
Tom Frith-Powellat work at the Paper Foundation
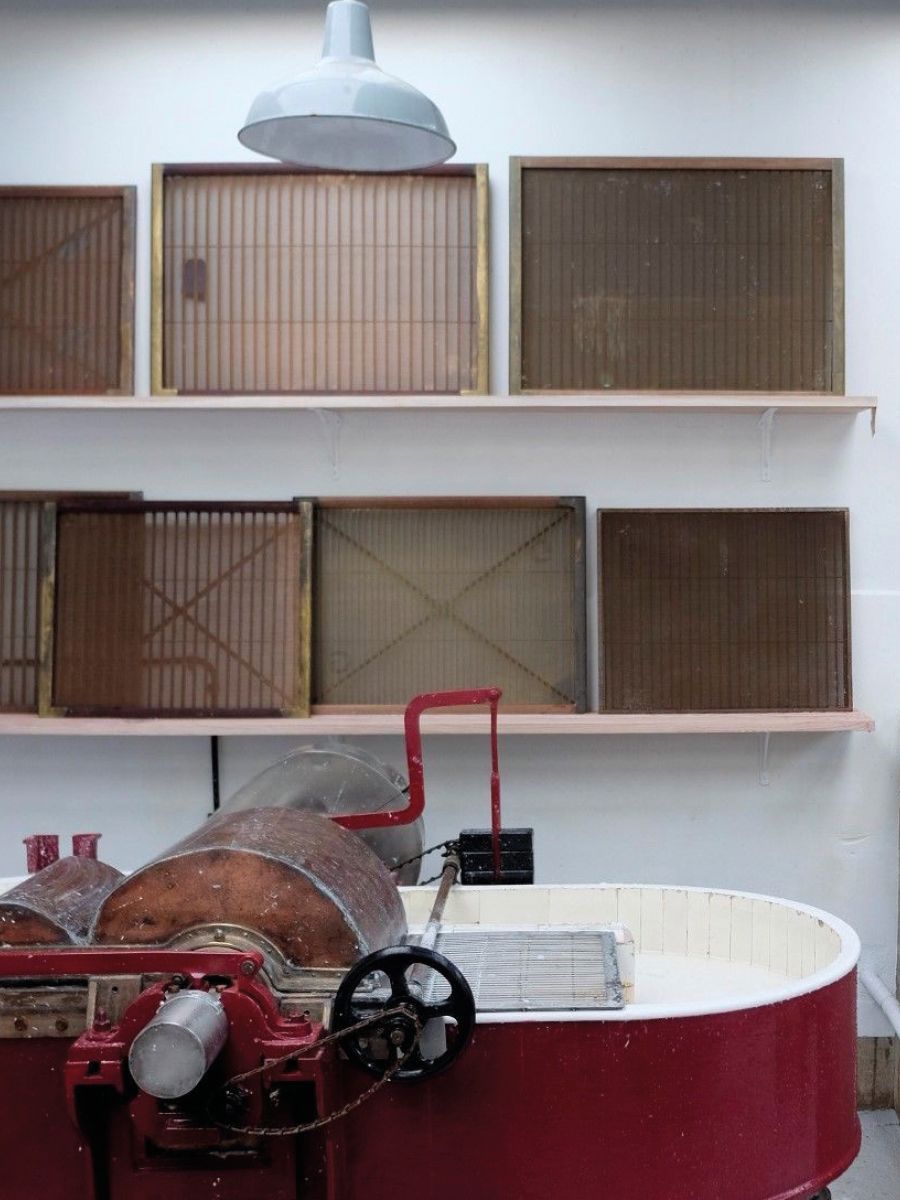
Tom Frith-Powellat work at the Paper Foundation
Tom Frith-Powellat work at the Paper Foundation
Powderhall Bronze
Sculptors Brian Caster and Kerry Hammond set up the Powderhall Bronze foundry in Edinburgh in 1989, having identified a gap in the market. A well-known local foundry had closed in the early 1980s and Scottish sculptors were having to travel to London to get their work cast. Their first building was a former bakery shop on the ground floor of a tenement block at the back of the Powderhall dog track. A local blacksmith told them that the Powderhall name derived from a gunpowder mill set up next to the Water of Leith c.1695. The name told customers of their original location and has a link to the work of the foundry, so it has stuck with them through four different locations to their current one in the Granton district of Edinburgh where they employ more than two dozen people.
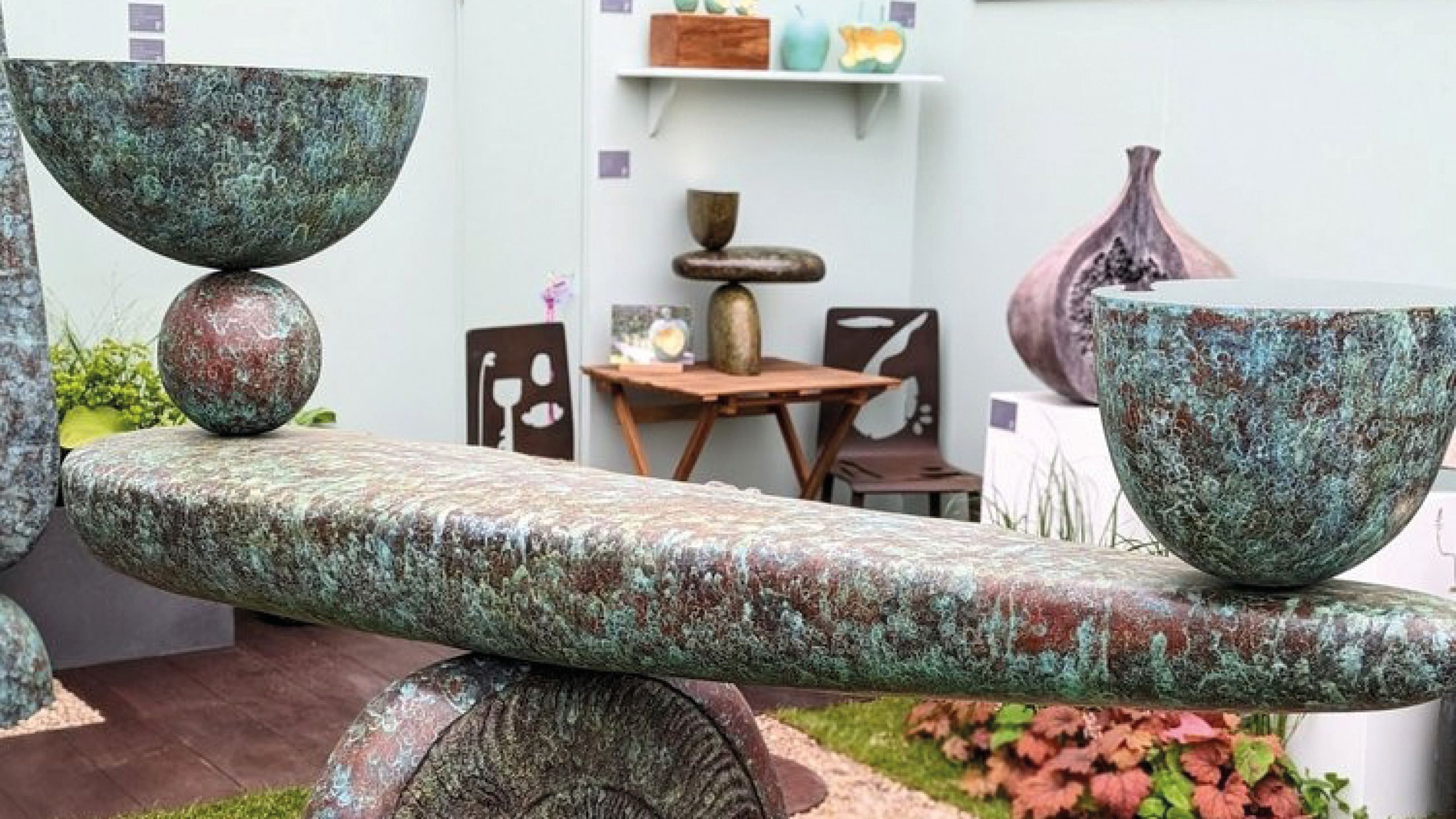
Caster and Hammond have built up the business through word of mouth into a leading fine-art foundry, creating unique sculptures for artists and commissioners worldwide. The foundry uses a variety of casting techniques: the lost wax process (well known to dental surgeons) using both Italian block moulding and ceramic shell and sandcasting. They also build armatures (frameworks for large pieces), carry out enlarging processes and provide a bronze cleaning and restoration service.
Bronze casts range in size from small, detailed pieces to large public sculptures. Once moulding is complete, a wax replica is made. Seams are worked using fine tools and soft modelling wax then the artist will check the wax sculpture and add their signature. Commissioners may also visit the foundry at this stage, as many like to be involved in the process. The foundry casts mainly in silicon bronze and also aluminium. The whole process from the arrival of the artist’s plaster or clay model to the final finishing of the bronze takes up to six weeks for a bust and three months for a life-size figure. The largest piece cast in bronze by the foundry is the Really Good sculpture by David Shrigley that was on the fourth plinth in Trafalgar Square, London, from 2017 to 2019: it was seven metres high and weighed five tonnes.
"They create unique sculptures for artists and commissioners worldwide"
In addition to fine art work, the team also undertakes the fabrication of quality railings and fittings for historic buildings, and the refurbishment and repair of sculptures throughout the UK. The foundry remade the spectacles for the Donald Dewar statue in Glasgow five times until the local council moved the sculpture to an unclimbable plinth.
Caster and Hammond continue to make their own work and have opened a gallery in Edinburgh where they show smaller pieces by a selection of artists, and 2D works including prints by their daughter, Lucy Caster. Their work can also be seen at the Chelsea Flower show as they have created a series of sculptures suitable for domestic gardens.
For further information about the foundry and gallery see www.powderhallbronze.co.uk